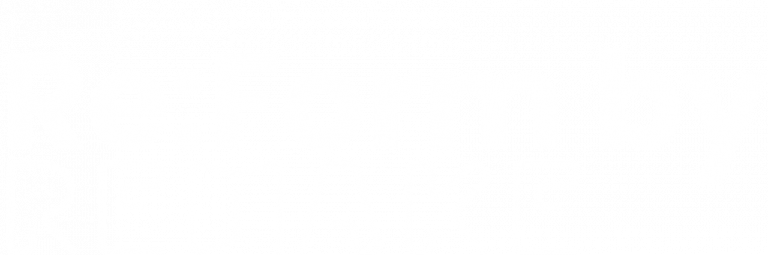
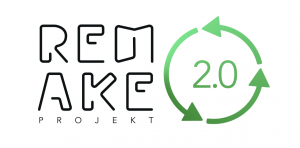
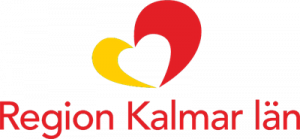
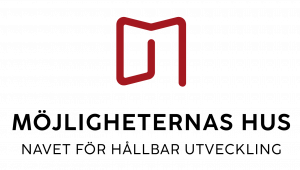
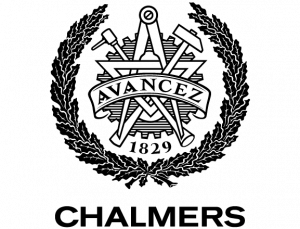
Creating products from industry waste
The Remake 2.0 project was initiated as part of a collaboration between Chalmers University of Technology, Möjligheternas Hus, Remake, Region Kalmar County and local businesses. The project aimed to develop innovative, sustainable products from industrial waste. The project sought not only to reduce environmental impact but also to engage individuals in job training at Remake, empowering them through meaningful work opportunities.
The Problem
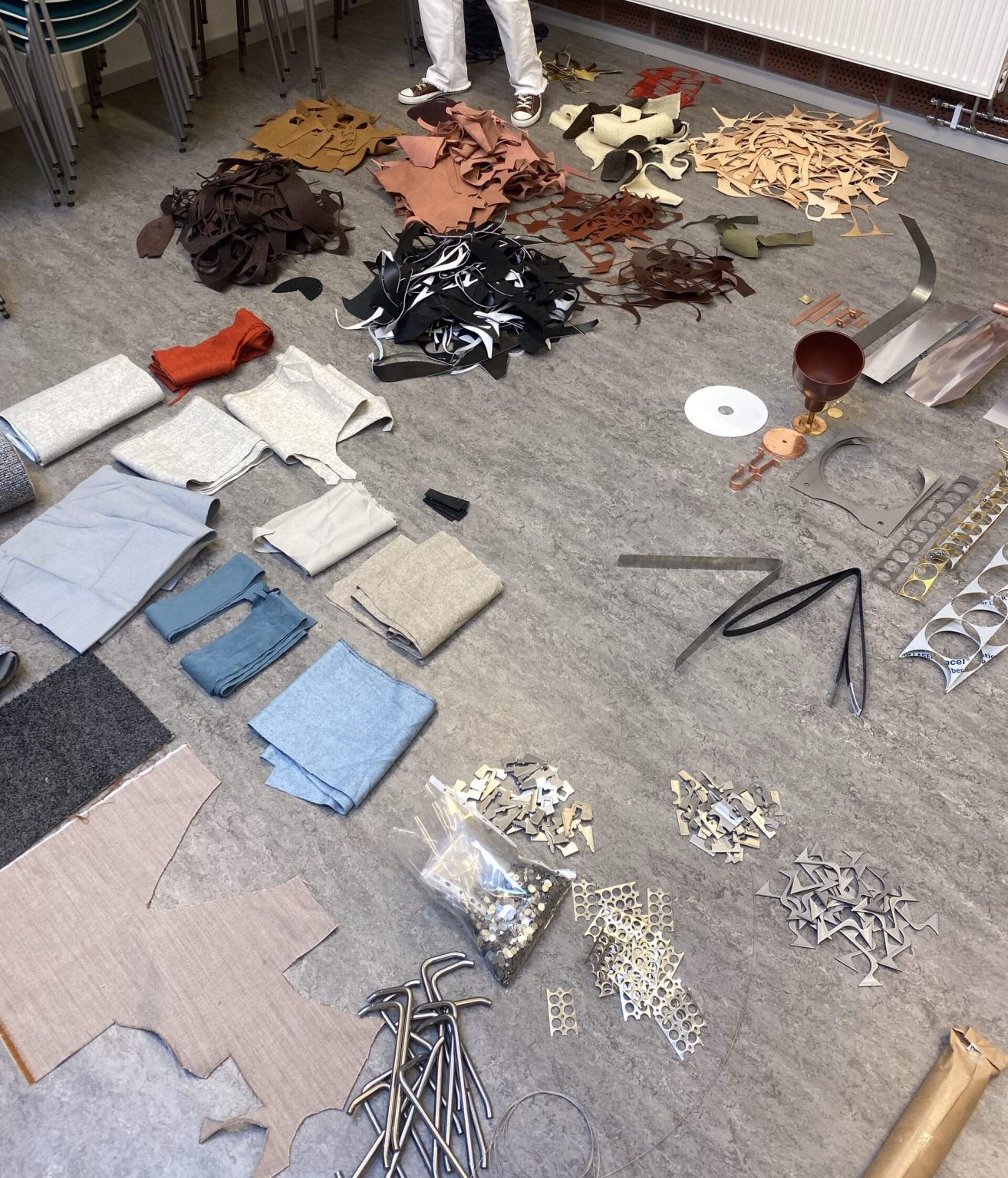
Approach
To address the problem, the project team reframed the initial brief, shifting the focus from developing a specific product to designing a versatile production process. The aim was to create a sustainable, scalable method that could handle various types of waste materials without needing to adjust for every irregularity. The solution was a process for melting and molding polypropylene plastic waste into uniform sheets, which could then be cut and assembled into a range of products.
The approach involved multiple stages:
Research & Experimentation
Material experimentation was a critical phase in understanding the potential of the various waste materials collected during the study visit to Möjligheternas Hus and partner companies. The team worked with a variety of materials, including textiles, wood, metal, glass, sawdust, and plastic, to explore their physical properties, processing techniques, and potential applications.
The experimentation phase revealed polypropylene plastic as the most viable material due to its adaptability, scalability, and alignment with the project’s goals of creating a versatile production process. Other materials, while intriguing, were either inconsistent in supply, difficult to process, or not feasible within the constraints of Remake’s facilities.
Why plastic sheets?
We chose plastic sheets because our experiments showed that plastic effectively addressed our challenges. Its ability to be remelted and reshaped allowed us to achieve consistent results across different shapes and sizes. Additionally, plastic’s wide availability ensures a stable material supply and offers exceptional design flexibility for creating various forms.
Plastic also brings valuable properties such as durability, water resistance, and strength. It is easy to work with and comes in a variety of colors and patterns. Most importantly, plastic is recyclable, making it a material that supports our sustainability goals.
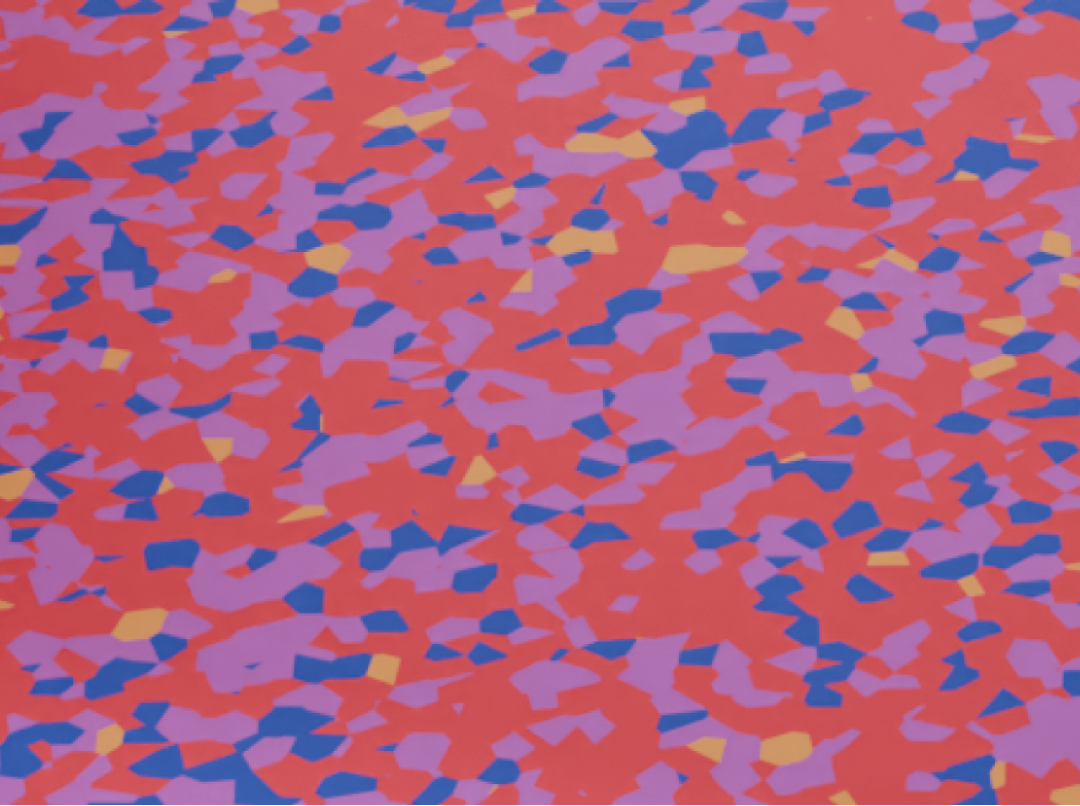
Co-creation and ideation
To ensure that the designs were aligned with both the material constraints and the skills of the job training participants, the team conducted a co-creation workshop. The participants generated ideas for products such as chairs, tables, storage solutions, and decorative items. Several brainstorming sessions and brainwriting techniques were used to expand on these ideas and filter them down to the most promising concepts.
Prototyping & Evaluation
Based on the ideas generated, prototypes of three main product concepts were created. The prototypes were evaluated based on criteria such as manufacturability, design expression, and ease of use. Adjustments were made, especially to ensure stability and structural integrity in the products, which were evaluated using both visual and functional assessments.
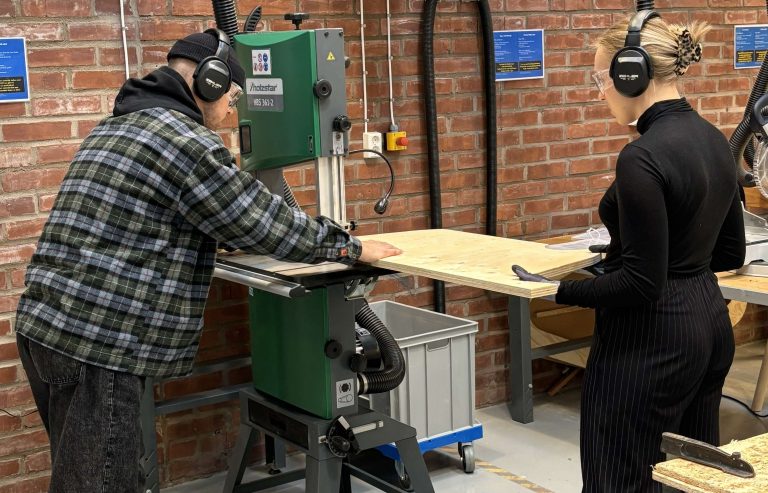
Instruction Development
Clear, visually supported instructions were developed to ensure the manufacturing process could be followed by participants with varying levels of experience. The goal was to make the process as intuitive as possible while providing educational value.
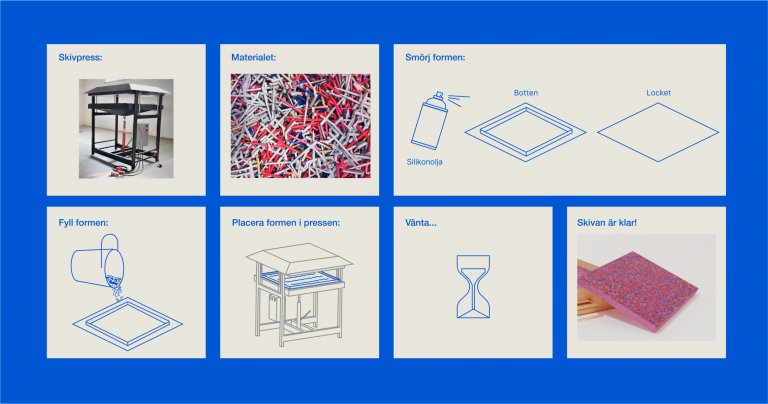
Output
Sittmöbel
A multifunctional seating solution that incorporates a magazine stand into its design, making it both practical and expressive. The design was appreciated for its bold, curated aesthetic and was well-received during the evaluation phase.
Pall
A four-legged stool with a dynamic design. It was rated highly for its modern, expressive look while still being easy to manufacture. The design was tweaked to ensure stability and ease of assembly, addressing issues with leg angles by adding a crossbar for support.
Tavla
Large decorative panels made from waste materials, designed to function as standalone art pieces. These panels allowed for a high degree of creativity in utilizing leftover materials and served as a versatile product for interior decoration.
Instruction Manuals for Production
Additionally, the project produced detailed, instructions that ensured all participants, regardless of their skill level or language proficiency, could understand the process. The instructions also fostered collaboration and learning within the Remake team, enabling participants to work together efficiently.Large decorative panels made from waste materials, designed to function as standalone art pieces. These panels allowed for a high degree of creativity in utilizing leftover materials and served as a versatile product for interior decoration.
Outcome
Environmental Impact
- The use of polypropylene plastic waste in the production process drastically reduced the environmental footprint compared to using virgin materials. Energy consumption for manufacturing was reduced by over 75%, and the carbon footprint for each product was halved.
- The repurposing of industrial waste not only minimized waste but also contributed to a more sustainable production cycle, with materials being reused or remelted into new sheets for future products.
Cost Effextiveness
- The use of free or low-cost waste materials resulted in a significant reduction in production costs—over 90% compared to using virgin plastic. This made the products more affordable to produce and more appealing to potential customers.
- The cost analysis showed that the break-even point for the products could be reached with a relatively low volume of sales, making the products viable for Remake’s long-term business model.
Social Impact
- The project provided valuable learning experiences for participants at Remake, helping them develop new skills in ideation and prototyping. By involving the participants directly in the process, they had the opportunity to help design the products they themselves will be producing – which was empowering to the participants.
- If this product goes to production, it will further provide learning opportunities in product design, manufacturing, and assembly, which aligns with the fundamental goals of Möjligheternas Hus.
Business Growth
- The project will serve as a good base for Remake to expand its product offerings and enter new markets, targeting a broader customer segment. The project resulted in a production process which enables a long term sustainable solution for Remake, both sustaniably and environmentally.
- A prototype website was developed, enabling Remake to engage a wider audience and establish a stronger brand presence.